Production
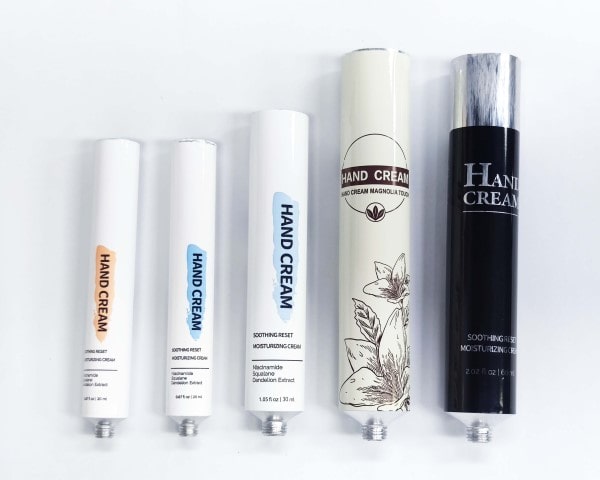
How Aluminum Collapsible Tubes Are Made
Now let’s delve into the aluminum collapsible tube manufacturing process, uncovering the key steps that transform aluminum slugs into the familiar, versatile containers we encounter daily.
Extrusion
At the heart of aluminum collapsible tube production lies the extrusion process. It all begins with high-quality aluminum slugs. Aluminum slugs are forced through a die, taking on the shape of hollow tubes. The size, thickness, and diameter of the tube are carefully controlled, ensuring uniformity and precision. Once extruded, these aluminum tubes possess the perfect foundation for packaging materials.
Trimming and Threading
The extruded tubes are then cut to their desired length, which corresponds to the final product’s size. Precision is key during this stage to maintain consistency across all tubes. Specialized machinery ensures smooth edges, and any excess material is removed, leaving clean, straight-edged tubes ready for further processing.
Annealing
Next, the tubes undergo annealing, a crucial step to enhance their structural integrity. Annealing involves subjecting the tubes to carefully controlled heat, which relieves internal stresses and increases their ductility. This makes the aluminum tubes less prone to cracking or breaking. Annealing also prepares the tubes for subsequent lacquering and coating, allowing these finishes to adhere effectively. (Reference: Why Are Aluminum Toothpaste Tubes Soft?)
Internal Lacquering
To prevent the contents of the tube from reacting with the aluminum, a protective internal lacquer is applied. This layer acts as a barrier, ensuring product integrity and longevity. The lacquer is evenly sprayed or rolled onto the inner surface of the tube, providing a safe environment for the contents it will soon hold. Internal lacquering is a pivotal step in maintaining the quality of the packaged product. (Reference: The Significance of Internal Lining in Hand Cream Aluminum Tubes)
Base Coating
Before moving on to the external finishes, the tubes receive a base coat on their outer surface. This base coat not only improves adhesion for subsequent printing and labeling but also acts as an additional layer of protection for the aluminum, enhancing corrosion resistance. The base coat is carefully applied and cured, setting the stage for the tubes’ final aesthetic enhancements and branding. (Reference: Base Coating for Aluminum Cosmetic Packaging Tubes)
Printing
Once the base coat has set, the tubes move on to the printing phase. This is where branding, product information, and decorative designs are applied to the outer surface. Advanced printing techniques ensure crisp and vibrant graphics that capture consumers’ attention on store shelves. Printing not only serves an aesthetic purpose but also provides crucial information about the product contained within, making it a vital step in the packaging process. (Reference: Mastering the Art of Tube Printing)
Baking
After printing, the tubes undergo a baking process to cure the inks. This ensures that the printed information and designs are firmly bonded to the tube’s surface, resistant to smudging or fading. Baking also contributes to the overall hardness and durability of the tube, making it capable of withstanding the rigors of transportation and consumer use.
Capping
Caps are pivotal that seals the tubes securely. The caps for aluminum tubes are typically made of plastic or metal, depending on the product’s requirements. They are carefully fitted onto the orifices of the tubes.
Latex Lining
In the final phase of manufacturing, the tubes undergo latex lining. This process involves applying a thin layer of latex to the inner surface of the tube’s opening. The latex lining serves a critical purpose: it creates an airtight seal once the tube has been folded and crimped. Lining helps preserve the freshness and integrity of the product, especially products that are sensitive to air, moisture and contaminants.
The meticulous journey from extrusion to latex lining transforms an aluminum slug into a versatile and reliable packaging solution. (Please click here for production photos from Xinyi Factory) These tubes play a crucial role in preserving the quality and usability of a wide range of products, from cosmetics to pharmaceuticals, and their manufacturing process showcases the intersection of precision engineering and creativity in the world of packaging. The next time you use a product from one of these tubes, you’ll have a deeper appreciation for the craftsmanship that goes into making them functional and visually appealing.
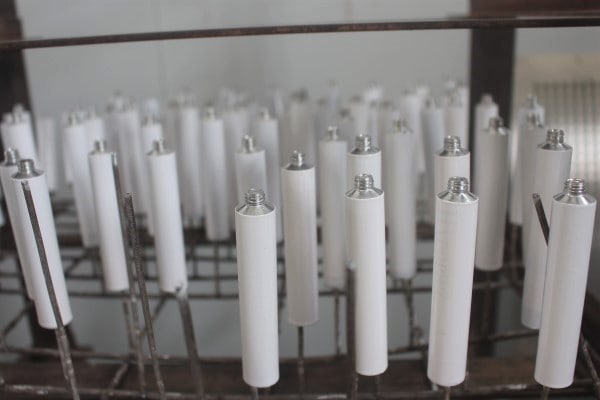
Request for Free Samples?
We offer FREE samples of aluminium tubes with pre-paid shipping and handling.
Send e-mail to Xin Yi and specify your preferred tube specifications.
We need your mailing address with zip code to get a quote for freight.
We accept PayPal payment for international sample shipping.
Quality assured production
We customize it!
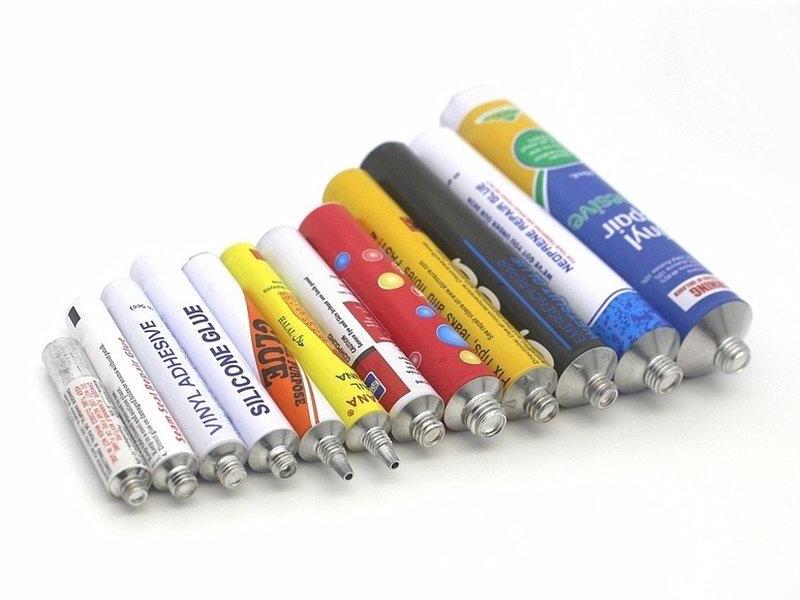
Multiple Dimensions
Xinyi offers aluminum tubes ranging from 8 mm to 32 mm diameter, holding 5 ml to 100 ml.
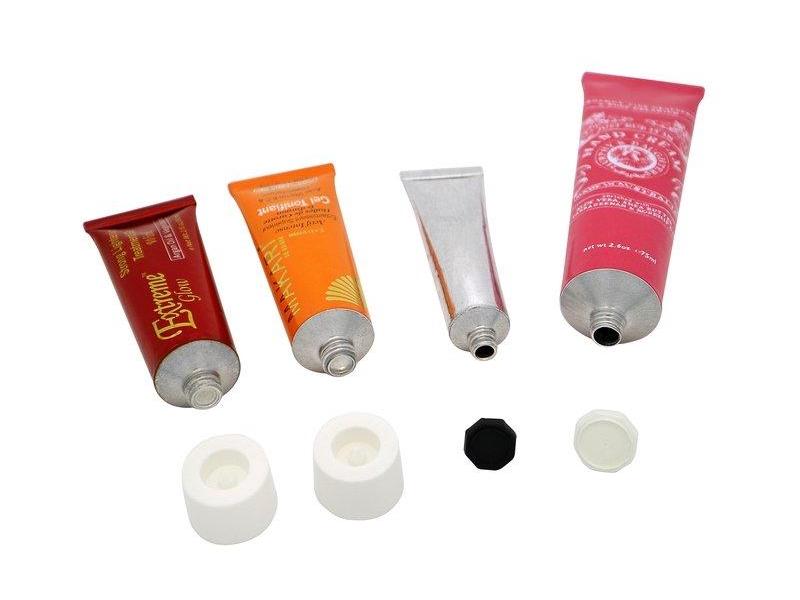
Custom Printing
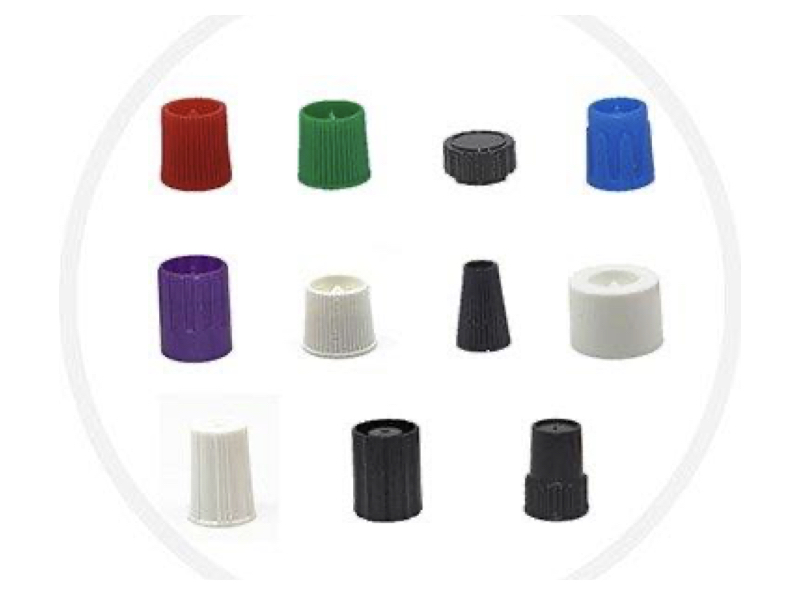
Moulding Service
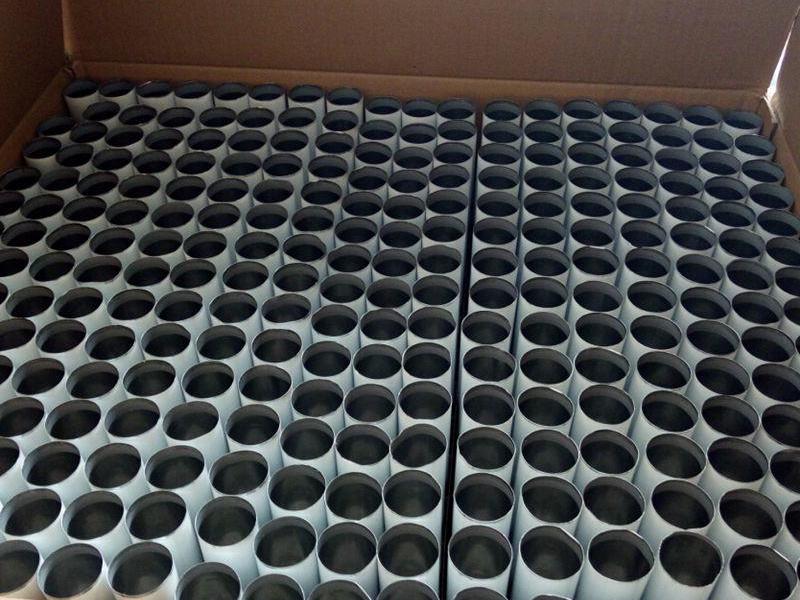